Transformação industrial acessível: chão de fábrica inteligente para PMEs
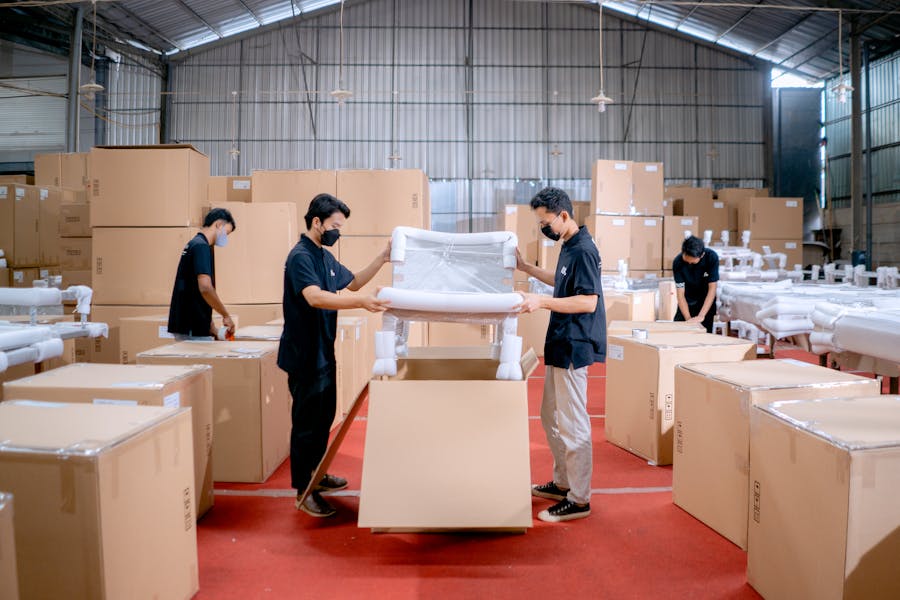
A transformação digital do ambiente produtivo não precisa ser privilégio apenas de grandes corporações. Com estratégias assertivas e implementação gradual, pequenas e médias indústrias podem modernizar seus processos de fabricação sem comprometer a saúde financeira. O caminho para um chão de fábrica conectado começa com passos estruturados e investimentos planejados.
Diagnóstico de maturidade digital: O ponto de partida estratégico
O processo de evolução tecnológica exige autoconhecimento organizacional. Antes de investir em qualquer solução, é fundamental realizar um diagnóstico completo da maturidade digital da operação. Este mapeamento inicial permite identificar não apenas as lacunas existentes, mas também as áreas onde os ganhos rápidos podem ser obtidos com mínimo investimento. Empresas do Segmento Metalmecânico com processos bem estabelecidos, por exemplo, frequentemente descobrem oportunidades imediatas na digitalização de controles de qualidade.
A avaliação estruturada contempla cinco dimensões fundamentais: infraestrutura tecnológica atual, qualificação da equipe, arquitetura de processos, gestão de dados e cultura organizacional. Cada uma destas áreas recebe uma classificação objetiva, permitindo a priorização de iniciativas conforme o contexto específico da indústria. Ao contrário do que muitos gestores imaginam, este diagnóstico frequentemente revela que os primeiros passos da transformação podem ser implementados usando recursos já existentes, apenas reorganizados de forma estratégica.
Implantação de coleta de dados estratégicos: Informação como alicerce da transformação
A base de qualquer ambiente produtivo inteligente está na capacidade de coletar e interpretar dados relevantes. O segredo está em identificar os pontos críticos onde a captura de informações gera máximo impacto com mínimo esforço implementacional.
Os principais dados estratégicos incluem:
- Indicadores de produtividade por estação de trabalho - Monitoramento do tempo real de processamento versus tempo planejado, identificando gargalos específicos
- Métricas de qualidade por lote - Registro digital de aprovações, rejeições e retrabalhos, vinculados a causas raiz codificadas
- Consumo real de matéria-prima - Confronto entre consumo teórico e efetivo, permitindo ajustes precisos em formulações e processos
- Tempos de setup e paradas não programadas - Categorização e quantificação de interrupções, criando base para melhorias sistemáticas
- Rastreabilidade de componentes críticos - Vinculação digital entre lotes de insumos e produtos acabados, garantindo segurança em eventuais recalls
{{cta}}
Automação de apontamentos de produção: O fim dos registros manuais
A substituição de papéis e planilhas por registros digitais representa um dos passos mais significativos na modernização do chão de fábrica. A troca de apontamentos manuais por sistemas integrados elimina não apenas o retrabalho de digitação, mas principalmente os frequentes erros de transcrição e atrasos na disponibilização das informações. Os ganhos imediatos incluem redução das horas administrativas, aumento da precisão nos dados de custos e disponibilidade imediata de informações para decisões táticas.
O sistema integrado permite que informações coletadas diretamente na operação alimentem simultaneamente múltiplos departamentos. Um único registro de produção atualiza automaticamente os módulos de custos, estoques, faturamento e planejamento, criando um fluxo informacional contínuo e consistente. Esta integração rompe as tradicionais barreiras departamentais, permitindo que áreas como comercial e financeiro tomem decisões baseadas em dados produtivos atualizados, não em estimativas ou informações defasadas.
Monitoramento em tempo real de indicadores críticos: Visibilidade para ação imediata
A disponibilização de métricas produtivas em tempo real representa um divisor de águas na gestão operacional. Ao contrário do modelo tradicional, onde indicadores são analisados dias ou semanas após os eventos, a visualização instantânea permite intervenções corretivas durante o próprio turno de produção. Este monitoramento pode começar com painéis simples, exibidos em monitores estrategicamente posicionados no ambiente fabril, e evoluir gradualmente para dashboards interativos acessíveis via dispositivos móveis.
Os principais elementos para implementação eficaz incluem:
- Seleção criteriosa de indicadores - Foco em 3-5 métricas essenciais para cada setor, evitando sobrecarga informacional
- Visualização adequada ao ambiente - Gráficos simples, cores contrastantes e indicações visuais claras de status (verde/amarelo/vermelho)
- Hierarquia de informações - Dashboards específicos para operadores, líderes e gestores, com nível apropriado de detalhamento
- Comparativos de desempenho - Exibição do desempenho atual versus metas e médias históricas, criando contexto interpretativo
- Alertas automáticos - Notificações para desvios significativos, permitindo ação proativa antes que problemas escalem
Integração progressiva com equipamentos existentes: Conectividade sem substituições onerosas
Um dos maiores receios de pequenas e médias indústrias ao considerar a digitalização é a necessidade de substituir maquinário existente por equipamentos com tecnologia embarcada. Na realidade, diversos métodos permitem conectar máquinas convencionais aos sistemas digitais sem investimentos proibitivos. A aplicação de sensores externos, coletores de dados e interfaces simplificadas possibilita que equipamentos tradicionais forneçam informações valiosas para o controle centralizado, estendendo sua vida útil enquanto participam do novo ambiente conectado.
Tecnologias acessíveis para modernização gradual
A transformação do ambiente produtivo pode ser implementada com ferramentas surpreendentemente acessíveis. Sensores de baixo custo, microcontroladores programáveis e aplicativos móveis customizados permitem automatizar a coleta de dados sem grandes desembolsos iniciais. O segredo está em priorizar áreas críticas e implementar soluções específicas que demonstrem retorno rápido, criando um círculo virtuoso onde cada melhoria financie a próxima etapa do processo.
Capacitação da equipe para a nova realidade
A adaptação do elemento humano ao ambiente digitalizado representa fator decisivo para o sucesso da transformação. O processo deve incluir não apenas treinamento técnico, mas principalmente a construção de uma cultura orientada a dados e melhoria contínua. Para pequenas e médias indústrias, a vantagem competitiva está na agilidade com que conseguem romper resistências naturais e converter operadores experientes em aliados da modernização. A abordagem inicial deve valorizar o conhecimento prático existente, demonstrando como as novas ferramentas potencializam - e não substituem - a experiência acumulada no chão de fábrica.
Acesso digital acessível para sua indústria
A jornada para um chão de fábrica inteligente começa com diagnóstico objetivo, coleta estratégica de dados e automação gradual de apontamentos. Esta abordagem progressiva permite que pequenas e médias indústrias colham benefícios concretos sem comprometer a saúde financeira do negócio. Para conhecer como sua operação pode iniciar esta transformação com investimento planejado e retorno acelerado, Entre em contato conosco!
Descubra como integrar todos os setores da sua indústria
Conheça as funcionalidades que podem acelerar sua produção em até 30% e reduzir custos
Elimine custos de produção e erros operacionais com o Methos Cloud ERP
Veja na prática como o Methos Cloud ERP pode ajudar a sua indústria a ser mais competitiva.
Apenas 20min. Sem compromisso.